30 Ton Heavy Lifting: Why 32 Tons Crane is Optimal
30 Ton Heavy Lifting: Why 32 Tons Crane is Optimal
A 32 ton overhead crane offers a safety margin for 30 ton loads, ensuring reliable operation, reducing stress, and enhancing longevity.
Overview of Heavy Lifting Needs in Industrial Applications
Heavy lifting is a crucial part of many industrial operations, where the safe and efficient movement of large and heavy materials is required to maintain productivity. In industries such as automotive manufacturing, construction, and general manufacturing, selecting the right lifting equipment is essential for both safety and operational efficiency.
The capacity of the crane determines the maximum weight it can safely lift, making it vital to match crane capacity with the weight of the loads to avoid overloading, which can lead to accidents, equipment failure, or even damage to the building structure. Choosing the correct crane ensures that the lifting process is completed without unnecessary strain on the crane, ultimately extending its lifespan and reducing downtime.
Common industrial applications requiring heavy lifting include:
- Automotive Manufacturing: In car assembly lines, cranes are used to move large parts such as engines, transmission systems, and body frames. These parts can easily weigh over 30 tons, requiring reliable cranes with sufficient capacity.
- Construction: In the construction industry, cranes are regularly used to lift heavy materials like steel beams, concrete slabs, and large machinery. These materials can exceed 30 tons, and cranes with the right capacity ensure the load is safely lifted without risking structural failure or accidents.
- General Manufacturing: Factories that handle large equipment or components, like industrial turbines or generators, often need cranes capable of lifting 30 tons or more to position these components for assembly or installation.
In all of these industries, the right crane capacity is not just about meeting the weight requirements of the load, but also ensuring that the equipment operates safely and efficiently in various environments.
Introduction to Overhead Cranes
An overhead crane, also known as a bridge crane, is a type of crane that is designed to lift and move heavy loads across a factory floor or a warehouse. It consists of a bridge beam that runs along tracks installed on the ceiling or high on the walls of the building, a hoist that lifts the load, and a trolley that moves the hoist along the bridge. Overhead cranes are widely used because of their ability to save space by operating above the ground and can handle large, heavy loads efficiently over long distances.
In heavy lifting operations, overhead cranes are ideal because they can move large and heavy items with ease. They are commonly used for tasks such as:
- Lifting and positioning large machinery and equipment.
- Moving bulky or irregularly shaped loads across an industrial facility.
- Performing repetitive lifting tasks on assembly lines or in warehouses.
The main advantage of using an overhead crane for heavy lifting is the precision and control it offers. The crane's design allows for accurate positioning of heavy loads, which is critical in industries like automotive and construction where exact placement is often required.
Overview of Different Crane Capacities in Industrial Settings
Cranes come in various capacities, designed to handle different types of loads and lifting needs. The most common industrial crane capacities range from small, light-duty models to large, heavy-duty systems capable of lifting hundreds of tons. In settings where heavy lifting is frequent, such as manufacturing plants or construction sites, cranes with higher capacities (such as 30 tons and above) are used for larger and heavier materials.
Some common crane capacities in industrial environments include:
- 1 to 10 tons: Ideal for lighter tasks, such as lifting smaller machinery or components.
- 10 to 20 tons: Used for moderate lifting tasks, such as moving large parts or machines in manufacturing facilities.
- 20 to 50 tons: Suited for larger equipment or multiple smaller components that need to be lifted together.
- Above 50 tons: These cranes are used in large-scale industrial operations, such as heavy construction, steel production, or shipbuilding.
In heavy lifting, a 32 ton overhead crane becomes an optimal choice. It offers just enough extra capacity to handle typical 30 ton loads safely while also providing the flexibility to lift slightly heavier materials if needed. The crane's design and features are tailored for the specific demands of industrial environments where safety, reliability, and efficiency are top priorities.
Selecting the right crane capacity is not just about ensuring it can handle the maximum weight of the load. It's also about having a safety margin to ensure that the crane operates within its optimal load range. This reduces the strain on the machine and helps avoid potential issues during operations.
Crane Capacity
What Does Crane Capacity Mean?
Crane capacity refers to the maximum weight that a crane can safely lift and support during operation. It is a key specification that determines the performance limits of the crane and is typically defined in tons. Understanding crane capacity is crucial because selecting a crane with the correct capacity ensures safe operations and prevents accidents caused by overloading.
The capacity is determined by several factors, including:
- Structural Strength: The design and materials used in the crane’s components (such as the hoist, bridge, trolley, and supporting structure) must be strong enough to handle the maximum weight of the load. The crane’s frame, gears, motors, and cables must all be designed to support the expected weight.
- Lifting Mechanism: The hoisting system, which includes the winch and pulley mechanisms, must be rated to lift the maximum load safely. The lifting speed, control system, and other operational aspects also factor into the crane’s overall capacity.
- Load Distribution: The way a load is distributed can impact the crane’s capacity. For example, if a load is not evenly distributed, it can create additional stress on the crane’s components, reducing its effective lifting capacity.
- Safety Factor: Crane manufacturers build in a safety factor, typically between 1.5 to 2 times the rated capacity, to ensure that the crane can handle unexpected stresses, such as wind or shock loading.
Proper crane capacity selection involves considering the maximum load weight you expect to handle, as well as the safety margin to account for additional stress on the crane during lifting.
Importance of Proper Capacity Selection for Load Safety
Selecting the right crane capacity is essential for load safety. If the crane's capacity is too low for the weight of the load being lifted, it can lead to serious safety risks, such as:
- Structural Damage: Overloading a crane can cause damage to its components, such as the hoist, motor, or the crane frame itself. This damage can be expensive to repair and may lead to extended downtime.
- Load Falling: If a crane is overloaded, the lifting mechanism may fail, causing the load to fall. This can result in severe injuries to workers, damage to materials, and even fatalities.
- Unstable Operation: Cranes that are working close to their capacity limits can become unstable, making it harder to control the load. This can lead to swinging loads, tipping, or other dangerous scenarios.
To avoid these risks, it’s essential to select a crane with the appropriate capacity for the task. This ensures that the crane can handle the expected load without being overworked, reducing the likelihood of accidents and ensuring the safety of both workers and equipment.
The 30-Ton Load Consideration
In industrial settings, a 30 ton load is a common weight that requires careful consideration. Loads of this size are typically found in industries like construction, automotive, manufacturing, and steel production, where large, heavy parts are regularly moved.
Common types of loads around 30 tons include:
- Automotive Parts: Large components like engine blocks, transmissions, or entire vehicle bodies can weigh 30 tons or more. Moving these parts in automotive assembly plants requires cranes with the right lifting capacity.
- Construction Materials: Steel beams, concrete slabs, and large prefabricated components used in buildings and bridges often weigh around 30 tons. These materials need to be lifted and positioned accurately on construction sites.
- Manufacturing Equipment: Large machinery such as industrial presses, turbines, or heavy stamping equipment can weigh in the range of 30 tons, requiring overhead cranes for installation and maintenance.
- Shipbuilding and Aerospace: Heavy parts used in the construction of ships or aircraft, such as fuselage sections, engine mounts, or heavy machinery, may also fall into the 30 ton weight category.
Handling 30 ton loads presents specific challenges, including:
- Load Control: Large and heavy loads, particularly those weighing 30 tons, can be difficult to maneuver. Without proper control, they can swing uncontrollably, creating safety hazards for workers and other equipment.
- Space Constraints: In many industrial settings, space is limited. Maneuvering a 30 ton load in tight areas requires precise operation of the crane, which can be challenging depending on the layout of the facility.
- Stability of the Load: Depending on the shape and design of the load, a 30 ton item may be unstable or difficult to balance during lifting. Loads that are irregularly shaped, such as steel beams or industrial components, require additional consideration to ensure they are securely positioned on the hook.
- Environmental Factors: The weight of the load combined with environmental factors like wind, vibrations, or even slight unevenness in the floor can complicate the lifting process. Cranes handling 30 ton loads must be designed to cope with these factors, especially when working outdoors or in challenging conditions.
- Safety Concerns: A 30 ton load has a significant potential to cause injury or damage if not handled properly. Ensuring that the crane is within its safe working limits, and that proper procedures are followed, is critical in avoiding accidents.
For these reasons, selecting the right crane for handling 30 ton loads is essential. Cranes with a higher capacity margin—such as a 32 ton crane—offer the necessary flexibility and safety to handle these loads efficiently and reduce the risks associated with heavy lifting.
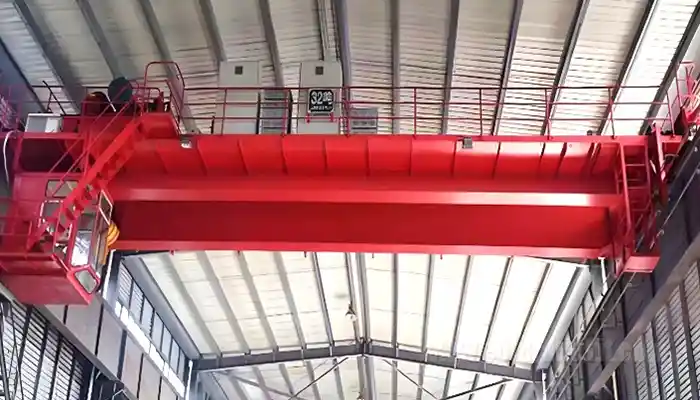
32 ton overhead crane for sale for heavy lifting
Why a 32-Ton Overhead Crane is Optimal for 30-Ton Loads
Safety Margin: The Role of Excess Capacity
A 32 ton overhead crane is an ideal choice for lifting 30 ton loads because of the additional safety margin it provides. The safety margin refers to the extra capacity built into the crane beyond the expected maximum load. This extra capacity is crucial for preventing the risks associated with lifting heavy loads, ensuring that the crane operates safely and efficiently without being stressed to its limits.
Explanation of Why a Slight Increase in Capacity (32 tons vs. 30 tons) Improves Safety:
When lifting heavy loads, the crane is subject to a variety of forces beyond just the weight of the load. These forces include:
- Dynamic Forces: These occur during lifting, lowering, and moving the load. As the crane hoists the load, acceleration, deceleration, and even sudden movements can place additional strain on the crane's components.
- Load Shifting: If the load shifts or sways while being lifted, it can create an additional moment of force on the crane, especially when handling large, bulky, or irregularly shaped items. This puts extra stress on the crane and can lead to instability.
A 32 ton crane has a built-in buffer that accounts for these dynamic and shifting forces. Having this extra capacity ensures that even under challenging conditions—such as quick starts and stops, sudden wind, or an uneven load—the crane won’t be pushed to its limits. This safety margin prevents the crane from being overstrained, which significantly reduces the risk of accidents like tipping, cable failure, or structural damage.
How a Safety Margin Helps Prevent Accidents from Overloading:
When a crane is operating at or near its rated capacity, it is much more susceptible to failure under unexpected conditions. For example:
- Overloading Risks: Operating a crane at full capacity increases the chance of exceeding the maximum load rating, especially when factoring in potential weight fluctuations or load shifts. This can lead to dangerous situations where the load may fall, or the crane components may fail.
- Overheating Motors: A crane that constantly works at or near its maximum capacity puts more strain on its motors, which can lead to overheating and, ultimately, motor failure.
A 32 ton crane offers an additional cushion of safety, helping to ensure that the equipment operates within a safe working load (SWL) range and reducing the likelihood of any unforeseen overload incidents.
Operational Efficiency and Longevity
Using a 32 ton crane to handle 30 ton loads doesn’t just improve safety—it also contributes to operational efficiency and the long-term longevity of the crane. This higher-capacity crane allows for smoother, more efficient lifting operations.
Benefits of Using a Crane with a Higher Capacity Than the Maximum Load:
- Reduced Stress on Crane Components: When a crane is used at its maximum rated capacity or slightly above it, every component—from the hoisting mechanism to the crane frame itself—operates under significant stress. Over time, this stress can cause wear and tear that leads to early equipment failure.
By selecting a 32 ton crane for handling 30 ton loads, the crane operates with less strain on its components, which results in reduced wear and tear. This leads to longer service life and fewer repairs, making the crane more reliable over time.
- Improved Performance Under Load: A higher-capacity crane generally has stronger motors, better stability, and more robust components. This allows the crane to operate more smoothly, with better control over the load, particularly during lifting, hoisting, and positioning. The crane’s components are not overburdened by high operational demands, leading to more efficient and consistent performance.
Reduced Wear and Tear on Crane Components Leading to Longer Lifespan and Lower Maintenance Costs:
The increased capacity reduces the strain on the crane's critical parts, such as the hoist, trolley, and motor. This means the crane is less likely to experience frequent breakdowns and requires fewer repairs. Over time, this leads to lower maintenance costs and higher operational efficiency. With fewer mechanical failures and reduced downtime, businesses can maximize productivity, making the initial investment in a 32 ton crane more cost-effective in the long term.
Flexibility in Handling Diverse Loads
One of the major advantages of opting for a 32 ton crane to handle 30 ton loads is its flexibility in handling a variety of loads, including loads that are slightly heavier or of varying shapes and sizes. This versatility can be a significant asset in industries that handle diverse loads on a daily basis.
A 32 ton Crane Can Handle Not Only 30-Ton Loads But Also Slightly Heavier Loads, Increasing Versatility:
- Handling Variations in Load Weight: In many industrial environments, the exact weight of the load can vary slightly due to factors like material density or weight fluctuations during the manufacturing process. A 32 ton crane can comfortably lift loads that are slightly heavier than 30 tons, allowing for a wider range of applications and reducing the need to switch cranes for different loads.
- Adaptability to Changing Needs: In facilities where the types of loads being lifted vary over time, having a 32 ton crane provides flexibility. Whether the load weighs 28 tons, 30 tons, or even 32 tons, the crane can handle it with ease. This eliminates the need for multiple cranes with varying capacities, streamlining operations and increasing overall productivity.
Accommodates Variations in Load Weight (e.g., Slight Discrepancies in Manufacturing Tolerances):
- Manufacturing Tolerances: In many industrial processes, there may be slight discrepancies in the weight of a product due to manufacturing tolerances. For example, a 30 ton part might weigh slightly more or less than 30 tons depending on how it was produced or assembled. A 32 ton crane provides the capacity cushion to lift such loads without concern for exceeding the crane's maximum rated load.
- Handling Irregularly Shaped Loads: Some loads, especially in industries like construction or aerospace, may be irregularly shaped or unevenly distributed. A 32 ton crane is more capable of handling these types of loads safely, as it can accommodate shifts in weight distribution and handle slightly heavier or bulkier items with greater ease.
By offering the ability to lift a wider range of load sizes, a 32 ton crane maximizes the efficiency of industrial operations, reducing downtime and increasing operational flexibility. This added versatility makes it a more valuable investment for companies that need to handle various types of loads across different stages of production.
Key Features of 32-Ton Overhead Cranes
Structural Design and Features
The structural design of a crane plays a crucial role in determining its lifting capacity, stability, and overall performance. While the basic framework of a 30 ton and 32 ton overhead crane may appear similar, key structural differences are designed to accommodate the higher load capacity of the latter.
Overview of the Structural Differences Between 30-Ton and 32-Ton Cranes:
- Frame Reinforcement: A 32 ton crane typically features reinforced beams and a stronger bridge structure compared to a 30 ton crane. This includes thicker steel components and additional bracing to ensure that the crane can safely support the additional weight and dynamic forces of a 32 ton load. The increased structural strength prevents flexing, bending, or warping of the crane frame under heavy loads, which is critical for long-term performance.
- Enhanced Rail Support: The overhead crane’s rails, which allow the crane to move across the span of the workshop or facility, are also reinforced in a 32 ton crane. These rails are often made from heavier, stronger materials or are bolstered with additional support to handle the increased weight.
- Hoist and Trolley Reinforcements: The hoist (which is responsible for lifting the load) and trolley (which moves the hoist along the bridge) are designed with additional strength and durability in a 32 ton crane. The trolley frame is often wider and the hoist drum larger, ensuring that the crane can handle the increased load capacity with stability.
- Motor and Drive System Enhancements: The crane’s motors and drive systems are designed to provide extra power and torque. A 32 ton crane may have larger motors or multi-speed drives that allow for smooth operation under heavier loads. This ensures better control and less strain on the crane’s mechanical systems, even at higher capacities.
Additional Reinforcements and Features in 32-Ton Cranes Designed for Increased Capacity:
- Stronger Supports and Joints: Connections between the crane's beams and joints are reinforced to bear the extra weight of a 32 ton load. These supports are designed with high-strength bolts or welds that maintain the crane’s structural integrity.
- Higher Load-Bearing Capacity for Wheels: The wheels that move the crane along the rail tracks must also be designed to handle the additional weight. 32 ton cranes feature wheels with larger diameters and stronger bearings to support the extra load, ensuring smoother movement and reducing wear on the tracks and wheels.
- Heavy-Duty Safety Features: For cranes with higher capacities, manufacturers often include enhanced safety features like overload protection, emergency brakes, and more robust limit switches. These additions provide extra protection when lifting heavy loads, ensuring that the crane does not exceed its safe operating limits.
Lifting Mechanism and Control Systems
The lifting mechanism and control systems in a 32 ton overhead crane are designed to offer enhanced precision and control, especially when handling heavy and delicate loads. These advanced systems ensure that the crane operates smoothly, even at higher capacities, reducing the risk of accidents and improving efficiency.
Lifting Mechanism Capabilities for Handling 30-Ton Loads with Precision:
- Hoist Design: The hoist mechanism in a 32 ton crane is built to handle heavier loads. The hoist motor is typically more powerful, with a higher lifting speed and capacity to handle not only 30 ton loads but also heavier items. This allows the crane to lift large and heavy objects with greater ease and precision.
- Heavy-Duty Wire Rope or Chain: A 32 ton crane is equipped with stronger wire ropes or chains that are rated for higher capacities. These ropes are typically thicker and more durable, reducing the risk of wear or breakage under heavy lifting conditions. The ropes or chains also feature improved lubrication systems to ensure smooth, safe operation.
- Load Distribution Mechanism: In cranes handling heavy loads, such as 30 tons or more, proper load distribution is key to maintaining stability and ensuring the crane operates within its safety limits. The hoist system in a 32 ton crane is designed with a balanced load distribution system, ensuring that the weight is evenly distributed across the crane’s components. This helps prevent the load from swinging or shifting unpredictably.
Advanced Control Systems for Smoother and Safer Operation at Higher Capacities:
- Load-Sensing Technology: One of the key features of modern overhead cranes is load-sensing technology, which helps ensure that the crane never exceeds its rated capacity. This system continuously monitors the load weight during lifting operations and provides real-time feedback to the operator. If the load approaches the crane’s maximum capacity, the system alerts the operator, preventing overload and reducing the risk of accidents.
- Variable Speed Drives: In a 32 ton crane, variable speed drives are used to control the hoisting speed, allowing for smooth acceleration and deceleration of the load. This is particularly important when lifting heavy objects, as sudden starts or stops can cause the load to shift or swing. By adjusting the speed based on the load’s weight and the crane’s capacity, the operator can achieve smoother, safer operation.
- Soft Start/Stop Features: Many modern 32 ton cranes come equipped with soft start/stop controls, which gradually increase or decrease the speed of the crane’s movements. This prevents jerky motions that could cause damage to the crane or its load. The gradual acceleration and deceleration reduce strain on the crane’s components and make it easier to position loads with high precision.
- Advanced Operator Control Systems: The control system of a 32 ton crane typically includes a digital interface with intuitive controls for operators. These systems may include remote control or wireless controls, which allow operators to move the crane from a safe distance. The digital interface can display real-time data, such as load weight, crane status, and diagnostic information, helping the operator make better decisions and ensuring smooth operations.
- Anti-Sway and Load Monitoring Systems: Cranes handling large loads like a 32 ton crane are often equipped with anti-sway systems that reduce the swinging motion of the load during lifting and transportation. These systems use sensors and control algorithms to detect and counteract any swaying, keeping the load steady and minimizing the risk of accidents or damage.
In summary, a 32 ton overhead crane is designed with enhanced structural reinforcements, more powerful lifting mechanisms, and advanced control systems to ensure that it can handle 30 ton loads safely, efficiently, and with precision. The combination of a stronger frame, advanced hoisting systems, and smart control technologies makes it an optimal choice for industrial operations where safety, longevity, and operational flexibility are paramount.
Cost-Benefit Analysis of Choosing a 32-Ton Overhead Crane
Initial Cost vs. Long-Term Savings
When considering the purchase of an overhead crane, it’s important to balance the initial cost with the potential long-term savings. While a 32 ton overhead crane may have a slightly higher upfront cost compared to a 30 ton crane, the benefits it provides over time can make it a more cost-effective investment in the long run.
Comparative Costs: 30-Ton vs. 32-Ton Overhead Cranes:
- Upfront Price Difference: The initial price difference between a 30 ton and a 32 ton crane is typically modest. While the 32 ton crane may cost slightly more due to its higher capacity and reinforced structural components, the difference in price is often not substantial when compared to the benefits it offers in terms of safety, flexibility, and durability.
- Investment in Quality: The additional cost of a 32 ton crane reflects the higher-quality materials and engineering involved in its design. Stronger components, more powerful motors, and advanced control systems all contribute to the price increase. However, these upgrades are designed to support heavier loads and provide greater reliability, which can result in fewer breakdowns and extended operational life.
Potential Long-Term Savings Due to Reduced Maintenance, Improved Safety, and More Flexible Use:
- Reduced Maintenance Costs: Over time, the slightly higher capacity of a 32 ton crane results in less strain on its components when lifting a 30 ton load. This reduction in wear and tear leads to fewer repairs, lower maintenance costs, and longer intervals between servicing. Cranes operating at or near full capacity experience more frequent breakdowns and may need more intensive repairs, whereas a 32 ton crane running under load will experience less wear, which contributes to cost savings over its lifespan.
- Improved Safety Leading to Fewer Accidents: A 32 ton crane provides a safety margin that helps avoid overloading and reduces the likelihood of accidents. With less risk of mechanical failure or accidents, businesses can avoid costly downtime due to accidents or repairs. Furthermore, reduced risk means fewer work-related injuries, which can result in lower insurance premiums and compliance with safety regulations. The improved safety features help to maintain a safe working environment, preventing the high costs associated with workplace injuries, litigation, or insurance claims.
- More Flexible Use and Higher Productivity: The versatility of a 32 ton crane allows it to handle a variety of loads, not just those weighing exactly 30 tons. This flexibility means that the crane can be used for different lifting needs across a variety of projects, without the need to invest in multiple cranes for different applications. For businesses with fluctuating lifting demands, this multi-purpose functionality translates into greater productivity and optimized equipment usage. The ability to handle slightly heavier loads with ease ensures that the crane can be used in a broader range of operations, avoiding the need for additional cranes to accommodate heavier items.
Return on Investment (ROI) for Businesses
Investing in a 32 ton overhead crane offers a range of benefits that contribute to a strong Return on Investment (ROI), especially for companies with heavy lifting needs. Although the initial cost may be higher, the long-term financial benefits often outweigh the extra upfront expense.
How Investing in a Slightly Higher-Capacity Crane Can Lead to Higher Productivity and Fewer Downtime Incidents:
- Increased Lifting Capacity for More Versatile Applications: A 32 ton crane not only handles 30 ton loads with ease but can also accommodate slightly heavier or irregularly shaped loads. This added flexibility increases productivity by allowing the crane to be used in a wider variety of applications, without needing to purchase additional equipment for heavier lifts. Whether it's for lifting heavy machinery, large parts in construction, or bulky components in manufacturing, a 32 ton crane ensures operations run smoothly and without delay.
- Fewer Downtime Incidents: Downtime due to equipment failure or crane maintenance is one of the most significant hidden costs in industrial operations. By selecting a crane with extra capacity, businesses experience fewer incidents of overload or component stress, which significantly reduces downtime. Scheduled maintenance becomes less frequent, and the crane experiences fewer emergency repairs. The more reliable and durable the crane, the less time it will spend in the repair shop, resulting in a more consistent operation and improved overall productivity.
- Efficiency Gains: A 32 ton crane can handle tasks with greater speed and precision, which means less time is spent on each lifting operation. The smoother control systems, faster hoisting mechanisms, and advanced safety features contribute to faster turnaround times for lifting and moving loads. This increased operational speed means that the crane can perform more lifts in a given period, further boosting productivity.
The Importance of ROI Analysis in Industrial Machinery Purchases:
Investing in industrial machinery, such as a 32 ton overhead crane, requires careful consideration of the ROI. ROI analysis helps businesses assess whether the potential gains—such as increased productivity, reduced downtime, and extended equipment life—justify the initial investment. To calculate ROI, businesses should consider the following factors:
- Upfront Costs: The initial purchase price of the crane, including installation and any customization or additional features.
- Operational Savings: Potential savings in maintenance, repairs, and energy costs over the lifespan of the crane.
- Productivity Gains: The improvement in operational efficiency and lifting capacity, leading to higher throughput and fewer delays.
- Safety and Risk Reduction: The reduction in accidents, which leads to fewer injury claims, lower insurance premiums, and compliance with workplace safety regulations.
By carefully evaluating these factors, companies can make an informed decision about whether the slightly higher initial cost of a 32 ton crane will ultimately yield a stronger ROI through enhanced productivity, fewer repairs, and greater safety.
In conclusion, the decision to invest in a 32 ton overhead crane offers businesses not only increased lifting capacity but also cost-effective long-term benefits. While the initial investment may be slightly higher, the savings in maintenance, the added flexibility, and the reduced downtime all contribute to a substantial return on investment. Ultimately, choosing a 32 ton crane provides a strong financial advantage and greater operational efficiency.
Case Studies & Applications
Case Study 1: Automotive Manufacturing Facility
In the fast-paced environment of an automotive manufacturing facility, precision, efficiency, and safety are paramount. The use of a 32 ton overhead crane in the assembly line allows for optimal performance in handling heavy automotive parts, such as engine blocks, transmission assemblies, and chassis components.
Application and Benefits:
- Handling Large Parts: The 32 ton crane provides ample capacity to lift not only 30 ton loads but also slightly heavier parts, ensuring that all parts of the assembly process are covered. Automotive manufacturing often involves handling large and irregularly shaped components, such as frames, engines, and body parts, which require a crane with additional lifting capacity.
- Flexibility in Load Handling: The flexibility of the 32 ton crane makes it ideal for handling varying weights and sizes, something particularly useful in just-in-time manufacturing environments. Whether it's moving heavy tooling equipment, assembling larger components, or lifting full assemblies, the crane's ability to handle slightly heavier loads reduces the need for additional machinery, enhancing overall operational efficiency.
- Safety and Reduced Downtime: The safety margin provided by the 32 ton crane ensures that the risk of overloading is minimized, leading to fewer accidents or breakdowns. This is especially crucial in automotive manufacturing, where any downtime in the assembly line can result in costly delays. The crane's reduced wear and tear also contributes to lower maintenance costs, ensuring uninterrupted production.
Case Study 2: Construction Site Heavy Lifting
On large construction sites, such as those building high-rise buildings, bridges, or other heavy infrastructure, cranes play a critical role in moving steel beams, heavy machinery, and other materials. A 32 ton overhead crane provides construction companies with the strength and versatility needed to handle these complex lifting tasks.
Application and Benefits:
- Steel Beams and Structural Components: At construction sites, particularly those focused on high-rise buildings, cranes are often required to lift heavy steel beams and other structural components weighing close to 30 tons. A 32 ton crane ensures that these heavy loads can be moved efficiently and safely, without the risk of overloading, while also accommodating any minor fluctuations in the weight of the materials.
- Handling Heavy Machinery: Construction sites also require the lifting and positioning of heavy machinery such as generators, compressors, and other equipment essential to the project. With its additional lifting capacity, the 32 ton crane makes it easier to move large equipment to and from different sections of the site, minimizing the need for multiple lifts and increasing project efficiency.
- Tough Environmental Conditions: Construction sites often involve challenging conditions, including uneven ground, tight spaces, and rough weather. The 32 ton crane is designed to operate smoothly under these conditions, offering enhanced stability and safety compared to smaller cranes, and ensuring that heavy loads can be moved without risking damage to equipment or workers.
Case Study 3: Aerospace Manufacturing
Aerospace manufacturing presents unique challenges due to the size, weight, and complexity of the components being produced. Aircraft parts, such as fuselage sections, wings, and engine components, often exceed the weight of typical industrial materials, requiring a crane that can safely handle these large loads while offering the precision needed to avoid damage.
Application and Benefits:
- Large Aircraft Components: In aerospace facilities, the 32 ton overhead crane is used to lift and move large components like fuselage sections, wing spars, and engine nacelles. These components often weigh close to or above 30 tons and need to be maneuvered with great care to avoid damage. The 32 ton crane ensures that the load is easily supported and moved with precision, even in confined spaces.
- Handling High-Value Components Safely: Aerospace parts are often highly specialized and expensive, making safety a top priority. The extra capacity of the 32 ton crane provides a safety margin that ensures that these sensitive parts are not overburdened during lifting. The advanced control systems and load-sensing technology in the crane help reduce the risk of accidents, ensuring that components are moved without risk of stress or damage.
- High-Precision Lifting: Precision is critical in aerospace manufacturing. The ability of a 32 ton crane to handle heavier loads while maintaining smooth, precise control ensures that components are placed exactly where they need to be during assembly, whether it’s in the aircraft assembly line or during maintenance and repairs. The flexibility of the crane, capable of lifting components of varying shapes and weights, enhances overall productivity while minimizing risk.
In conclusion, the 32 ton overhead crane is indispensable in industries such as automotive manufacturing, construction, and aerospace, where heavy lifting, precision, and safety are top priorities. Its extra capacity, flexibility, and advanced features make it ideal for handling a range of challenging loads, ultimately leading to higher efficiency, reduced downtime, and improved safety in the workplace.
Safety Considerations and Standards for Heavy Lifting
Crane Load Testing and Certification
When operating a 32 ton overhead crane or any heavy lifting machinery, it is crucial to ensure that the equipment is safe, reliable, and capable of handling the required loads. This is where load testing and certification play an essential role in maintaining operational safety and meeting industry standards.
Importance of Load Testing and Certification for Cranes Operating at or Near Their Maximum Capacity:
- Load Testing: Load testing involves subjecting a crane to a series of controlled tests to verify that it can safely lift loads up to its rated capacity and beyond. For a 32 ton crane, the load testing process will typically involve lifting a series of progressively heavier loads, ensuring that the crane operates within the limits of its design specifications. These tests are conducted to ensure that the crane's lifting mechanisms, structure, and control systems function properly without risking failure under heavy load conditions.
- Safety Margin Validation: A 32 ton crane is designed to lift loads of up to 32 tons, but when operating near maximum capacity, additional safety precautions must be in place. Load testing ensures that the crane can handle extreme conditions (such as maximum rated loads, environmental factors, and operational stress) while maintaining structural integrity. This is particularly important when lifting 30 ton loads or heavier, as cranes are often subjected to wear and tear during repeated heavy lifting.
- Certification: After completing load testing, the crane must be certified to verify that it meets national and international safety standards. Certification typically involves a detailed inspection by an authorized inspector, who will review the crane’s design, materials, and operational capacity. Certification ensures that the crane is legally compliant with industry standards, such as the ISO 9001 (quality management) or EN 15011 (overhead travelling cranes) standards. It also confirms that the crane is ready for safe use in a variety of industrial environments.
- Legal and Insurance Requirements: Many industries have legal requirements for cranes operating at or near their maximum rated capacity to undergo periodic load testing and certification. This not only helps to meet safety regulations but is also necessary to maintain insurance coverage. In the event of an accident or equipment failure, having certified equipment can protect the company from liability issues.
Industry Standards and Safety Regulations for 32-Ton Overhead Cranes:
- OSHA Standards: In the United States, the Occupational Safety and Health Administration (OSHA) sets guidelines for the safe operation of cranes in the workplace. According to OSHA regulations, cranes must be inspected regularly, and operators must ensure that cranes are not overloaded beyond their rated capacity. For a 32 ton crane, adherence to these regulations ensures that all lifting activities are carried out in a manner that minimizes risks to workers and equipment.
- European Union (EU) Standards: In the EU, overhead cranes are subject to the Machinery Directive (2006/42/EC), which sets out safety requirements for machinery used in industrial operations. This directive applies to cranes used for lifting heavy loads, including 32 ton cranes, and mandates rigorous design and construction standards to ensure safety. Compliance with these standards is vital for companies operating in EU-member states to avoid penalties and ensure safe crane operation.
- ISO Standards: The International Organization for Standardization (ISO) provides globally recognized guidelines for cranes. ISO 4301 and ISO 9001 are essential standards for overhead cranes, ensuring that they meet safety, design, and operational criteria. The ISO 4301 standard specifically addresses classifications of cranes, including load capacity, which would be relevant when operating a 32 ton crane.
Maintenance and Inspection for Safe Operations
Regular maintenance and thorough inspections are key to ensuring the safe operation and longevity of a 32 ton overhead crane. Cranes used for heavy-duty lifting must be kept in peak condition to prevent accidents, breakdowns, and costly repairs.
Regular Maintenance Best Practices for Heavy-Duty Cranes:
- Lubrication and Moving Parts: Regular lubrication of moving parts (e.g., hoists, trolley wheels, and lifting gears) is crucial to ensure smooth operation and prevent wear from friction. The frequency of lubrication depends on the crane’s operating environment, but it should be conducted regularly according to the manufacturer’s guidelines. Under-lubrication can lead to excessive wear and failure of critical components, particularly in cranes handling 30 ton loads or more.
- Hydraulic and Electrical Systems: The hydraulic and electrical systems of the crane are essential for lifting and controlling heavy loads. Scheduled inspections should include checking for leaks in the hydraulic lines, ensuring proper fluid levels, and testing electrical components such as control panels, motors, and wiring. Faulty systems can lead to unsafe lifting conditions and operational delays.
- Structural Inspections: A thorough inspection of the crane's structure is essential to identify any signs of stress or damage, particularly when operating near maximum capacity. Inspections should focus on load-bearing components like the crane's beams, lifting blocks, and shackles. Cracks, corrosion, and other signs of wear can compromise the crane's safety and should be addressed immediately. For a 32 ton crane, regular inspections help to catch potential issues before they become significant failures.
- Testing of Safety Features: Safety features, such as limit switches, emergency stop buttons, and overload protection systems, should be tested regularly to ensure they function properly. A malfunctioning safety system could lead to accidents and injuries, especially when lifting near maximum capacity. Emergency response drills should also be conducted to ensure that operators are familiar with the crane’s safety protocols.
Tips for Ensuring the Safety and Longevity of Cranes Used for 30-Ton Loads and Heavier:
- Avoid Overloading: One of the most important ways to ensure the safety of a 32 ton crane is to avoid consistently operating it at or above its rated capacity. Overloading a crane places unnecessary stress on its components, reducing its lifespan and increasing the likelihood of mechanical failure. It’s crucial to always work within the crane’s rated capacity, even with a safety margin built in.
- Operator Training and Certification: Operators should be thoroughly trained and certified to operate a 32 ton crane safely. Proper training ensures that operators understand the crane’s features, load limits, and the best practices for safe lifting. Certified operators can identify potential issues and respond effectively in case of an emergency.
- Record Keeping and Documentation: Keeping accurate records of inspections, maintenance, and repairs is critical for tracking the crane’s condition and ensuring that all necessary work is done on time. Documentation serves as proof of compliance with safety regulations and can help identify patterns of wear or recurring issues that require attention.
In summary, ensuring the safe and efficient operation of a 32 ton overhead crane requires a comprehensive approach to load testing, certification, maintenance, and inspection. Adhering to industry safety standards and implementing regular maintenance practices not only ensures the longevity of the crane but also significantly reduces the risk of accidents, contributing to a safer working environment. Through proper maintenance, training, and safety measures, businesses can optimize the performance of their cranes, protecting both workers and equipment from potential harm.
Conclusion
Throughout this guide, we've highlighted why a 32 ton overhead crane is the optimal choice for handling 30 ton loads in various industrial settings. The key reasons for choosing a crane with slightly higher capacity include:
- Safety: The 32 ton crane provides an essential safety margin, ensuring that it can handle heavy loads without the risk of overloading. This margin prevents mechanical failures and enhances the crane's stability during lifting operations, reducing the potential for accidents.
- Efficiency: A crane with a higher lifting capacity, like the 32 ton model, leads to greater operational flexibility. It can accommodate varying load weights, including slight discrepancies in the weight of materials or components. This versatility helps improve efficiency and productivity, particularly in high-demand industries like automotive manufacturing, construction, and aerospace.
- Longevity: By operating within the optimal load range and avoiding consistent maximum capacity lifts, a 32 ton crane experiences reduced wear and tear, ultimately leading to lower maintenance costs and a longer lifespan for the crane’s components.
When selecting a crane for heavy lifting tasks, it’s crucial to consider not only the immediate requirements but also the long-term needs of your business. While a 30 ton crane may seem sufficient, opting for a 32 ton crane provides added benefits that ensure your equipment can handle future challenges and accommodate a variety of load types with ease.
Investing in a slightly higher-capacity crane is a smart decision that offers long-term value. It allows businesses to avoid potential operational bottlenecks, ensures that safety is prioritized, and contributes to a more resilient and efficient operation.
Ultimately, selecting the right crane capacity is about balancing immediate lifting needs with the flexibility to manage unforeseen challenges, ensuring that your business remains competitive, safe, and efficient in the years to come. Therefore, investing in a 32 ton crane isn’t just about lifting heavier loads—it’s about future-proofing your operations and reducing risks associated with equipment failure or unsafe lifting conditions.
Appendix (Optional)
FAQs about 30-Ton and 32-Ton Overhead Cranes
1. Why is a 32 ton crane better than a 30 ton crane for handling 30 ton loads?
A 32 ton crane offers a safety margin that helps prevent overloading and ensures smoother operations, especially when handling loads close to the maximum rated capacity. This added capacity protects the crane’s components, improves operational stability, and reduces the risk of accidents or equipment failure.
2. Can a 32 ton crane handle loads heavier than 30 tons?
Yes, a 32 ton crane is designed to handle loads up to 32 tons, making it suitable for lifting both 30 ton loads and slightly heavier materials. This flexibility increases the crane’s versatility in handling a variety of load weights, making it ideal for diverse industrial applications.
3. How often should a 32 ton crane be maintained?
A crane’s maintenance schedule depends on factors such as usage frequency and environmental conditions. However, regular inspections should be conducted at least every 6 months or after every 1,000 lifting hours to check for wear and tear. Preventive maintenance ensures safe operations and extends the crane’s lifespan.
4. Is a 32 ton crane suitable for all industries?
Yes, a 32 ton crane is versatile and can be used in a wide range of industries such as automotive manufacturing, construction, aerospace, and shipbuilding. It is ideal for handling heavy loads, such as steel beams, machinery, and large components, while ensuring safety and efficiency.
5. How do I know if my crane is overloaded?
Overloading a crane can be identified by signs such as straining noises, slower operation, or unusual movement. Modern cranes often feature load sensors or overload protection systems that can alert the operator if the load exceeds the crane’s capacity. Always ensure the crane is used within its rated load limit.
Glossary of Key Terms
- Crane Capacity: The maximum weight a crane can safely lift. For example, a 32 ton crane can lift up to 32 tons of weight, with additional safety margins built in for safe operation.
- Safety Margin: An additional capacity beyond the maximum rated load that ensures the crane operates safely under normal and unexpected conditions. For instance, a 32 ton crane has a safety margin when lifting 30 ton loads, reducing the likelihood of overloading.
- Load Testing: A process in which a crane is subjected to various loads (often above its rated capacity) to ensure it can handle heavy lifting operations safely without failure.
- Overload Protection System: A built-in safety feature designed to prevent the crane from lifting loads beyond its maximum rated capacity. This system typically involves sensors or limiters that alert operators when the load exceeds safe limits.
- Hoist Mechanism: The component of a crane responsible for lifting and lowering the load. It typically includes a motor, rope, and winch system to raise or lower materials efficiently.
- Load-Sensing Technology: Advanced systems that monitor and adjust the crane’s lifting mechanism to ensure the load is within safe operating limits, providing smooth and efficient control during lifting operations.
- Overhead Crane: A type of crane that operates above a fixed track or beam, allowing for the lifting and moving of heavy loads across a defined path. These cranes are commonly used in industrial settings such as factories and warehouses.
- Structural Reinforcements: Modifications or additional support in the crane's frame and components that allow it to safely handle higher loads or operate under more demanding conditions.
- Lifting Block: A pulley system used to change the direction of the crane’s lifting cable. It is an essential part of the hoisting mechanism, helping to lift and lower loads with precision.
- Trolley: A component that moves along the crane’s beam or track, carrying the hoist and load across the workspace. The trolley is typically motorized to ensure smooth travel.
- Inspection Checklist: A detailed list used during routine inspections to verify the crane’s components, including lifting mechanisms, structural integrity, and safety features, ensuring they meet required standards and are in good working condition.
Article by Bella ,who has been in the hoist and crane field since 2016. Bella provides overhead crane & gantry crane consultation services for clients who need a customized overhead travelling crane solution.Contact her to get free consultation.